高质量的产品正以前所未有的速度从设计到生产再到市场
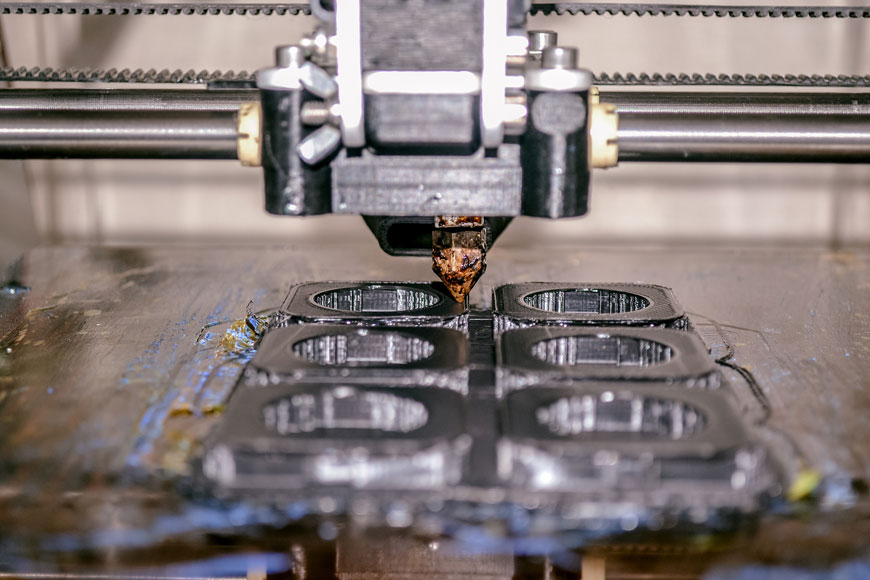
将一种新产品引入市场涉及到设计、市场研究和制造的复杂过程。快速原型是这个过程的一部分,在这个过程中,为了开发产品的工作模型,部件被制造出来——测试它的功能和局限性。这些原型可以由与最终产品相同的材料制成,或者可用于测试用例目的的替代材料。
金属原型的一些方法包括:
- 3D打印
- 砂型铸造(木纹)
- 熔模铸造(蜡模)
- 直接用金属坯料制造零件
- 直接从金属坯料加工零件
快速成型方法及应用
每个原型化方法都具有其优缺点,以及使其最适合某些项目的因素。
3D打印
3D打印是一种相对较新的工艺,也被称为增材制造,即一次打印一层产品,直到由多层产品组成3D组件的过程。每一层大约100微米厚。该打印机由一个计算机化系统控制,以3D设计作为输入,并创建3D产品作为输出。
随着时间的推移,技术不断发展,各种各样的材料已经可以用于印刷。塑料、尼龙、树脂、银、钛、钢、蜡、光聚物和聚碳酸酯都可以用作3D打印材料。
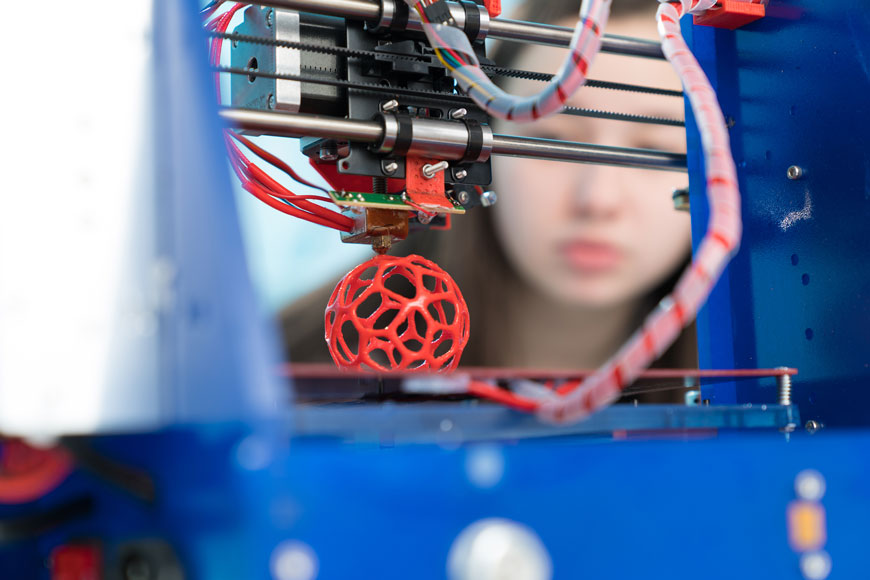
3D打印机主要有三种类型:
- 选择性激光烧结(SLS)使用粉末形式提供的印刷材料。零件的每一层都是用激光熔化粉末制成的。新鲜的粉末滚在刚完成的部分上,然后这个过程再次开始,直到整个部分完成。
- 熔融沉积建模(FDM)使用热塑性丝状并将其熔化用于挤出。挤出由计算机精确地控制根据3D设计,连续打印每层。
- 有限元也使用激光,但在这种情况下,液体产品通过激光作用一次固化一层——它被控制以符合设计。
3D打印是流行的快速原型,因为这个过程是非常资源高效的。生产线不需要工具,劳动力需求最小,产生的浪费很少。3D打印的缺点是,它可以花费时间-需要几个小时,有时几天,以构建复杂的部件。零件尺寸受机器印刷面积的限制。此外,由于某些金属的熔点很高,可能无法用所需材料生产零件。
砂铸造
在金属铸造厂,图案用来制造用来铸造金属零件的模具。原型模式以最简单和最具成本效益的方式制作,以便在必要时对零件进行测试和调整。由于这个原因,这个图案经常被用来制作砂型,因为这是最便宜和最快的模具生产。从开始到完成,一个原型可以在2到4周内使用松散的木制图案。
松散的木质图案是由一名制模师使用诸如车削、工具、模具制作和精细的木材加工等技术从木材中制作出来的。该图案是根据原型设计制造的,带有一些内建的收缩公差,这发生在金属冷却。当原型设计要求有回抽的零件时,这些零件被制成由销固定在适当位置的松散零件。
型砂是由正确的成分混合而成,因此具有金属铸造所需的特性。它必须保持它的形状,不释放太多的水分,并给予一个良好的质量。沙子被包裹在松散的木质图案周围形成一个铸件,然后可以用来制作金属原型。
铸造金属原型是一种标准铸造工艺,其中金属熔化,将组合物控制,熔融金属倒入模具中。一旦冷却,模具就会破灭,金属原型已准备好完成。
金属铸造由于生产成本低,且在必要时调整图案和重新铸造相对容易,木质图案的快速原型很受欢迎。用最终产品相同的材料制作原型也是可能的,这样就省去了后续的开发步骤。制造商经常发现,开发原型的过程往往成为最终生产的方法,只需要稍作修改。
熔模铸造
熔模铸造也是一种金属铸造工艺,但使用不同的技术使图案为创建模具。第一步是创建与原型设计相匹配的蜡样。历史上,蜡模是用注塑机或蜡压机制作的,但新材料和3D打印的发展为熔模铸造创造了机会,使其更加容易和快速。
一旦图案制作完成,它就会被套在陶瓷材料中,随着图案的形成,陶瓷材料就会呈现图案的形状。然后加热模具,直到蜡融化并流出铸造模具——因此它的另一个名字是失蜡铸造。标准的铸造工艺是将熔化的金属浇注到铸件中。当金属冷却和凝固后,陶瓷铸件被切断,留下金属原型准备完成。
这种快速成型的方法的优点与那些松散的木制图案相似——附加的好处是更精细的公差和饰面。
制造金属原型
库存金属材料包括床单,杆,管道,杆和电线。其中任何一个都可以用作制造金属原型作为下游二级步骤的原料,而不是通过诸如铸造或3D印刷的主要制造。
对于钣金原型制造,可以采用许多不同的工艺来制造原型。例如,物理模型可以被压平并放置在金属板上作为模板,然后激光或火炬可以用来切割轮廓和开口,并标记弯曲。可以使用压力机在有标记的边界处弯曲金属,还可以使用专门的焊接设备将零件连接在一起。
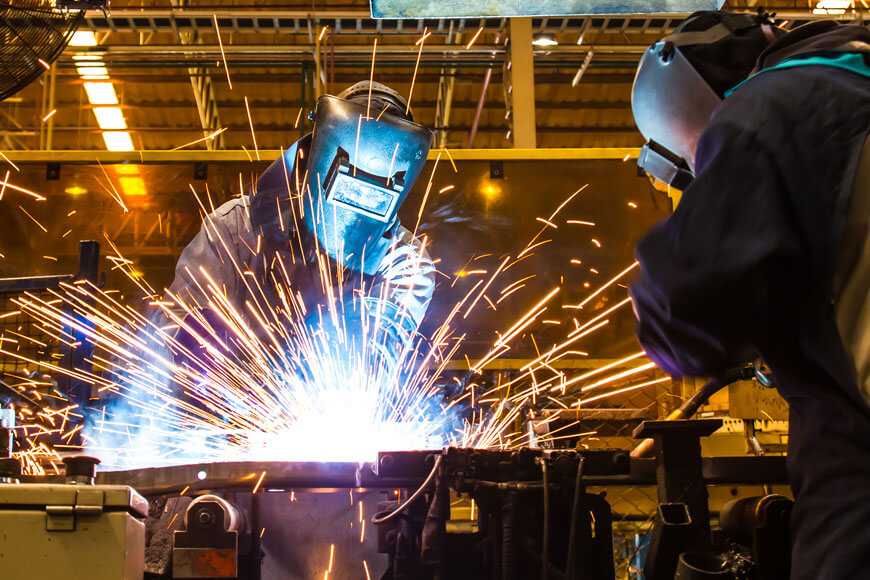
油管可用于原型,通过一系列不同的操作来处理它,以创建一个匹配设计的原型部件:
- 扩口-将管道末端的开口扩大为漏斗形
- 发型-减少或增加油管的直径
- 起涟漪- 金属表面上的小变形
- 弯曲-通过在油管中定义的点插入弯管来创建形状
- 压扁-使用压力机压缩油管
- 穿刺-在材料上制造孔
- 扩大-使用加热和工具打开油管的直径
制造股票材料的金属原型的主要优点是时间效率。不需要图案或模具,并从架子上提供原料。缺点是一些原型设计对于标准制造工艺来说太复杂,因此不能用这种技术进行。
加工金属原型
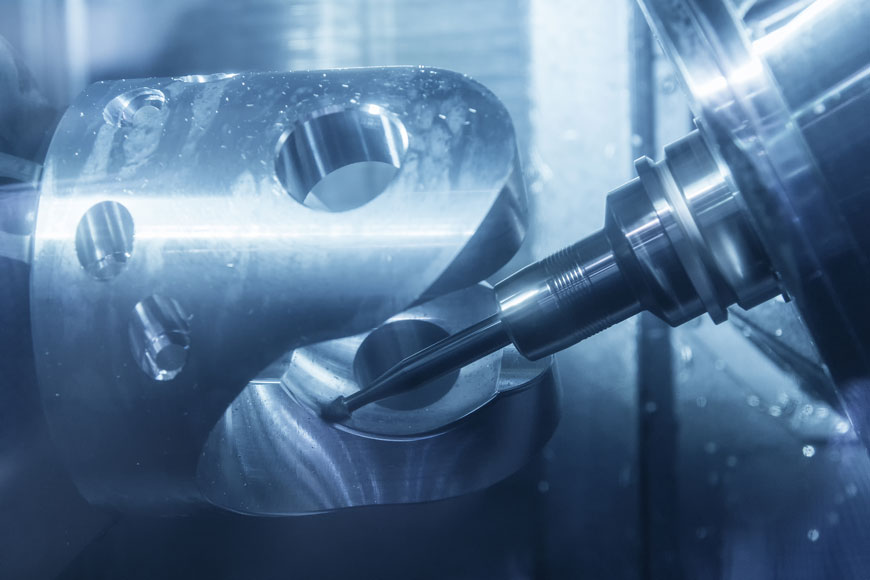
机械加工是通过受控的材料去除过程将原材料切割成所需的最终形状和尺寸的任何过程,也称为减法制造。它可用于制造各种金属制品,以及木材、塑料、陶瓷、复合材料等材料。在现代生产中,加工是通过计算机数控(CNC)来进行的。
CNC是根据3D设计制作一部分的加工设备的计算机化控制。加工设备包括车床,铣床,路由器,钻头和磨床。CNC机器的原料是钢板和钢板等货币制品。
3D设计转换为计算机程序,然后由控制系统使用,以指示机器。选择的原料必须大于所制造的原型,因为它是通过加工制造原型来除去金属。先进的CNC机器控制所有3轴(x,y和z)的操作,可以自动翻转零件和开关加工工具,从而高质量的表面处理和精度水平。
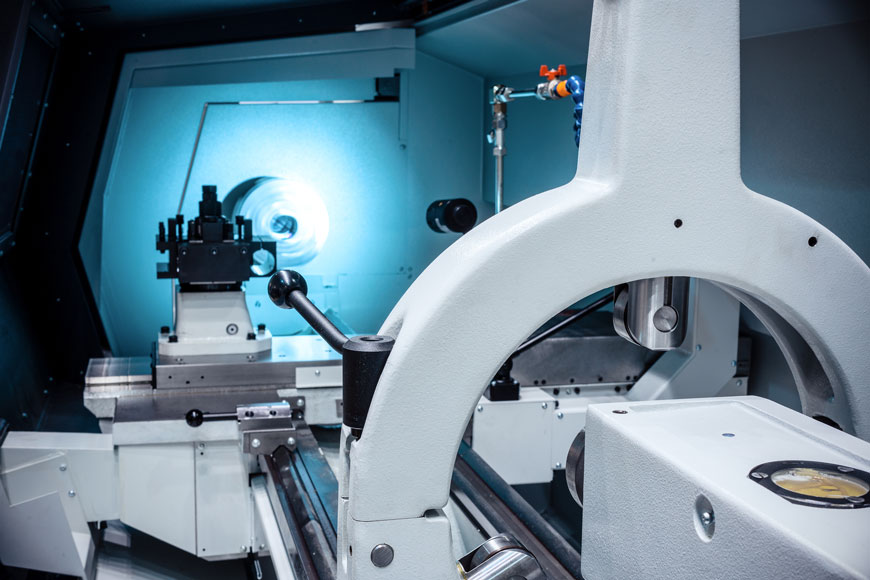
与其他制造技术相比,数控机床的优势是基于3D设计的自动化动作。人工干预是有限的,制造的原型与设计匹配的精确度很高。使用数控机床可以制造出比手工操作更复杂的原型。机械加工零件的一个缺点是该零件是通过从原材料中去除金属而制成的,这就导致了浪费。虽然废料可以回收利用,但会产生成本影响和损失。
快速原型案例研究
汽车工业
研究表明,3D印刷的发展对工程师能力进行了巨大影响,以快速地将产品带到市场上。一个汽车的文章强调了测试某些汽车部件的空气动力学是衡量其对汽车性能的影响的关键。随着测试结果的获得,可以对设计进行微小的调整,新的原型很快就可以重新印刷。在空气动力学测试中,用最终材料制造零件并不重要,因为测试的是形状,而不是强度。3D打印技术正在帮助汽车工程师加快开发和提高效率。
不同的应用适用于不同的制造方法。在一个例子中,一位设计师发现了这一点当制造两部分环组件时,内部空间中有micro SD卡的空间。第一个原型是由直接金属激光烧结(DMLS)制造的,但较低质量的表面光洁度和糟糕的组装导致了使用静电放电加工的数控机床的研究。样机性能的改善突出了CNC在这一具体应用中的优势。
高新技术产业
降低发展成本是许多高科技公司的经济要求,因为他们将新创作带到市场。当图标飞机为他们的A5休闲飞机推出该项目时,他们投入了大量的时间和精力,以寻找最具成本效益和有效的方式,以构建原型制作和批量生产的组件。案例研究表明,通过减少对专业工具的需求,在生产时间表,2000美元和每个空气管道部门的两人和两个人的图标飞机上涨。
飞机制造工业
美国铸造协会奖2017年度最佳演员被授予一家公司,为飞机乘客座椅框架开发了一种新的铸件。从历史上看,这种结构部件是由单个钢坯制成的,但经过详细的设计和工程处理,最终形成了一种由镁制成的晶格结构。镁是一种比铝轻的材料,但无法通过3D打印实现。铸造原型生产出的产品具有所需的强度,但比现有的机加工部件轻得多。一架客机每年节省10万美元的计算是根据由于更轻的座椅而减少的燃料费用以及相关的减少排放。
快速成型和前方道路
越来越多的方法快速原型制造可供创新者和工程师使用。每种方法都有自己的优点和缺点。铸造工艺适用于原型必须以与成品相同的材料制成的应用,特别是对于高熔点金属。3D打印适用于特定可印刷材料制成的较小部件 - 该技术正在持续开发和改善。加工可用于从储备产品中切除金属,其中复杂性不是太严重,并且仍然可以使用铣削和研磨等标准过程。
詹姆斯·戴森爵士是一位标志性的发明家、企业家和工程师,最著名的是他开发的旋风真空系统,在家庭清洁系统中取代了袋式真空系统。在一个迷人的采访BBC戴森透露,他的发明花了5年时间来完善,总共进行了5127次不同的调整和修改。他坚信一句古老的格言:“如果第一次你没有成功,尝试,再尝试!”Dyson的故事强调了这样一个事实:产品开发人员和工程师需要多次迭代的开发和改进才能将新产品推向市场。对快速原型的改进将继续降低效率和成本,使创新者和消费者都受益。
参考文献
- 3单。”3 d打印技术基础知识”
- 马林钢。”3D打印与传统制造”
- 机械的发明。”类型的模式”
- 机械工程。”造型图案/砂型铸造图案/图案和模具”
- miBot。”制作砂型和图案”
- 制造业图书馆。”投资铸造”
- 铸造管理与技术“,””让投资成为更好的投资”
- 托马斯净。”更多关于数控加工”
- 快速的金属板。”快速原型制造”
- 创新机制。”所有你需要知道的数控机床”
- 维基百科。”加工”